Применение 3D печати в процессах промышленного литья
Промышленность является приоритетной сферой применения аддитивных технологий. Именно здесь полностью раскрывается высокий потенциал послойного синтеза.
Литье под давлением
Литье под давлением или инжекционное литье — процесс впрыска пластичного материала (чаще всего это термопластики) в полость пресс-формы, где он, остывая, затвердевает. Такой вид литья широко применяется в промышленности во всем мире. Чаще всего его используют в массовом производстве точных деталей как достаточно простых, так и сложных форм. Цикл на средние по размеру детали занимает от 20 до 40 секунд. В результате получается готовое изделие или элемент конструкции.
Сроки выхода новой продукции на рынок определяют экономический успех всего проекта и его рентабельность. Подготовка нового изделия к крупносерийному производству сопровождается длительным процессом отработки многочисленных технологических режимов. Ведь последующее массовое изготовление деталей должно иметь четкий такт выпуска. Процесс отработки и внедрения требует значительных трудовых, временных и, конечно, финансовых затрат. И вполне закономерно желание любого производителя сократить затраты на этом этапе.
Сегодня все чаще литьевые формы, изготовленные способом 3D-печати, используются для создания опытных образцов деталей с целью выявления возможных проблем с геометрией или проверки функциональных характеристик будущего изделия. Зачастую прочностных возможностей такой формы вполне достаточно для проведения расчетов усадки и отработки режимов производственного цикла.
Раньше для изготовления тестовой оснастки с целью проверки параметров литья под давлением единственным вариантом были пресс-формы из алюминия, как мягкого и легко обрабатываемого материала. По сравнению со стальными аналогами изготавливались они быстрее и стоили дешевле. Тем не менее затраты и сроки оставались по-прежнему высокими, не говоря уже о конструкторских и технологических геометрических ограничениях. Например, цена изготовления небольшой пресс-формы может варьироваться от ста пятидесяти тысяч до полутора миллионов рублей, и это без учета затрат на оперативную доставку пресс-формы, если ее изготовление осуществляется сторонней фирмой. При этом весь процесс занимает в лучшем случае два месяца, а, как правило, — в пределах четырех-шести месяцев.
Эти факторы, безусловно, напрямую отражаются на экономической эффективности проекта подготовки выпуска нового изделия. В результате такие вынужденные инвестиции для большинства компаний становятся просто неподъемными. И, естественно, затраты возрастают всегда, когда требуется (а так обычно и бывает) малейшее изменение формы. В этих условиях многие производители вынуждены отказываться от перспективных проектов в связи с ограниченным бюджетом, что тормозит их развитие и ослабляет позиции на рынке.
Безусловно, лучшим вариантом для оценки геометрии, дизайна и оценки функциональности литьевых форм являются сегодня образцы, распечатанные на 3D-принтерах. С их помощью можно изготовить от 5 до 100 конечных деталей. Очень важно, что эти детали будут сделаны из материала, который используется непосредственно при серийном производстве. Их изготовление займет всего 1-2 дня, что значительно сокращает время изготовления литьевых форм по сравнению с традиционными методами. При использовании для изготовления пресс-форм технологии PolyJet от компании Stratasys производители могут быстро и экономически эффективно оценить формообразующие детали и их действительную производительность в предполагаемом технологическом процессе.
Основные преимущества технологии PolyJet, которые делают ее незаменимой в производстве литьевых форм:
- высокое качество. Высочайшее разрешение этого метода послойного синтеза (толщина слоя составляет от 14 мкм) позволяет получать модели с высоким уровнем детализации;
- высокая точность. Точный впрыск и свойства материала позволяют получать модели с высокой точностью и тонкими стенками (0,6 мм и менее в зависимости от геометрии и применяемого материала);
- экологичность, простота эксплуатации и обслуживания. Возможность применения в офисном помещении, отсутствие контакта с жидким фотополимером, легкое удаление поддержек и простая замена головок;
- скорость. Быстрое изготовление моделей благодаря высокой скорости печати, возможности печати сразу нескольких деталей и отсутствию необходимости в процедуре дополнительного отверждения;
- универсальность. Широкий выбор моделирующих материалов, удобство, легкость и скорость их смены позволяют получать детали с различными механическими свойствами, геометрией и цветом. При этом материал поддержек для всех типов модельных фотополимеров может быть один и тот же.
При изготовлении литьевой оснастки для литья под давлением мы рекомендуем использовать материалы Digital ABS и Digital ABS2. Объясним, почему.
Материал Digital ABS образован композитным смешиванием материалов RGD515 и RGD535, он предназначен для имитации стандартных пластмасс ABS. Он сочетает в себе стойкость к высоким температурам и высокую прочность. Digital ABS2 обладает теми же свойствами, а также повышенной жесткостью и прочностью при необходимости использования стенок деталей толщиной менее 1,2 мм. Оба материала подходят для производства деталей по технологии PolyJet, обеспечивая высочайшую ударопрочность и демпфирующую способность полученных изделий.
Возможность использования 3D-печати в инжекционном литье применяют и уже высоко оценили мировые компании-брэнды: Nypro Healthcare, Grundfos, Seuffer, Berker, Rutland Plastics Limited и др. Так, например, Berker является ведущим немецким разработчиком и производителем высококачественных электронных коммутаторов и интеллектуальных систем управления зданиями. Компания завоевала множество наград за качество своей продукции, широко используемой по всему миру. Основная задача, стоявшая перед компанией — тестирование нового электрического компонента, который содержит детали, изготовленные литьем под давлением. После сборки детали должны были проходить специальные испытания. Важно, что прототип, например, электрического переключателя должен был быть изготовлен из тех же материалов, что и конечное изделие.
Вместо того чтобы использовать инжекционные металлические формы для проверки конструкции, дорогостоящие и отнимающие много времени на их производство, специалисты Berker решили попробовать модели, напечатанные по технологии PolyJet. Одной из самых больших проблем было то, что вновь разработанные детали должны были работать совместно с уже существующей металлической оснасткой в отлаженном процессе. Компания выпустила серию напечатанных пресс-форм для литья под давлением и использовала для этого материал DigitalABS. Каждая форма обладала уникальной геометрией, и была использована для литья в них таких материалов, как ASA, PC и TPE.
Гибкий технологический процесс дал возможность попробовать несколько различных вариантов конструкций для получения наилучшего результата в очень короткий промежуток времени. Удалось оперативно получить необходимые сертификационные тесты, подтверждающие качество продукции. Экономия времени и денежных средств оказалась на уровне фантастических 83-85%!
Таким образом, применение технологии PolyJet позволило компании Berker успешно решить свои задачи путем 3D-печатания форм, которые были использованы для получения литьевых моделей с соответствующими допусками и с возможностью работы с конечным материалом. В результате Berker успешно и в короткие сроки запустил очередной модельный ряд продукции в серию.
По достоинству оценили технологию PolyJet и отечественные производители. Так, например, на Ижевском мотозаводе «Аксион-Холдинг» для подготовки производства и повышения его эффективности применяют современные аддитивные технологии.
Цели, которые они преследуют, близки любому производителю:
- замена материала оснастки на более технологичный;
- сокращение времени и затрат на подготовку производства, а также на эксплуатацию металлообрабатывающего оборудования;
- обновление парка оборудования.
Началось с того, что специалисты предприятия столкнулись с потерями времени на стадии подготовки производства, достигающими 67% от общего цикла производства. Мелкосерийное производство при столь дорогостоящей оснастке является нерентабельным, что и стало причиной поиска ими более гибких и современных технологических решений.
«Аксион-Холдинг» обратился в компанию «Современное оборудование», обладающую большим опытом реализации комплексных проектов по поставке и применению промышленного оборудования для 3D-печати. Специалисты «Аксион-холдинг» поставили перед нами следующие задачи:
1. Снижение времени и стоимости изготовления малых партий деталей из пластмасс, полученных методом литья под давлением.
2. Снижение трудоемкости изготовления деталей, получаемых литьем в землю.
3. Снижение времени и стоимости изготовления малых партий деталей из металлов с помощью литья по выплавляемым (выжигаемым) моделям.
4. Снижение времени и стоимости изготовления сборочной оснастки.
Несмотря на разноплановость этих задач, нам удалось справиться со всеми при помощи аддитивных технологий, предлагаемых «Современным оборудованием». В рамках решения первой задачи наши специалисты провели проектные работы по выбору варианта ее технологического решения. Снижение времени и стоимости изготовления малых партий деталей из пластмасс «Оправка», полученных методом литья под давлением предполагалось осуществить применением 3D-печати по технологии PolyJet. Совместно с зарубежными партнерами был выбран оптимальный вариант изготовления и напечатаны элементы пресс-формы «Оправка». Трудоемкость изготовления составила всего 4 нормо-часа, тогда как при используемой на предприятии традиционной технологии пришлось бы затратить 32. В данную оправку было отлито 20 деталей из полиэтилена ПЭ15803-020 ГОСТ16337-77 (давление литья 30-35кг*см3,температура литья 230оС) и полиамид ПА6-210-КС ОСТ6-11-498-79 (давление литья 60-65 кг*см3, температура литья 260оС). Запланированный экономический эффект был с легкостью достигнут, а сокращение сроков подготовки производства составило 87%.
«Аксион-Холдинг» и далее планирует использовать 3D-печать для решения своих задач, опираясь на возможности компании «Современное оборудование». Таких задач становится все больше, поэтому организация планирует приобрести в будущем собственную установку для быстрого прототипирования.
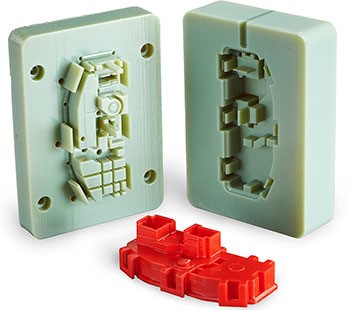
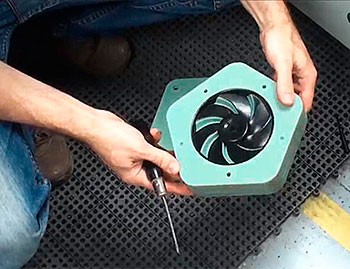
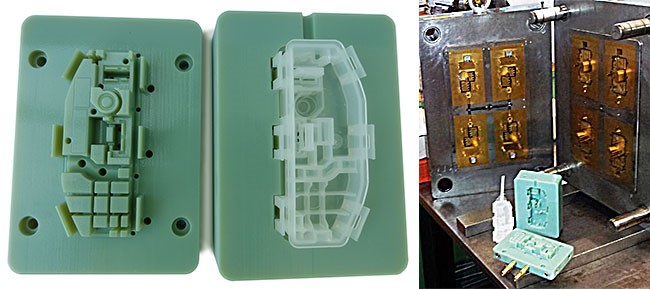
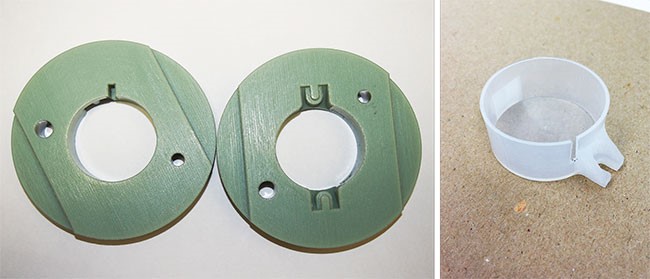
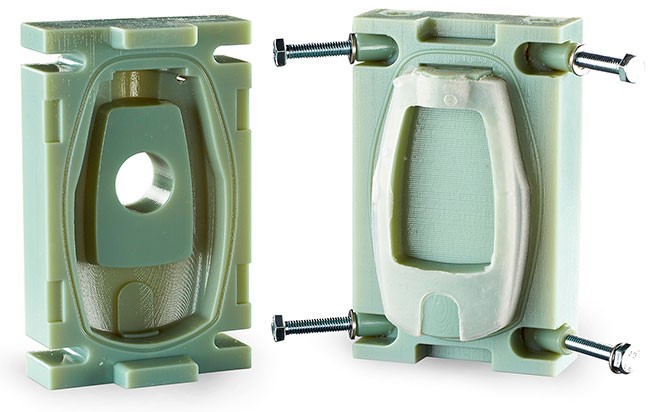
Литье в силиконовые формы
В последнее время набирает популярность мелкосерийное литье в силиконовые формы. Когда необходимо изготовление крупных партий пластмассовых изделий (десятков и сотен тысяч), то оптимальным решением в плане финансовых и временных затрат является литье в традиционные металлические пресс-формы. Однако что делать, если требуется производство деталей небольшими сериями? Так как изготовление традиционной пресс-формы в этом случае чрезмерно дорого и длительно, оптимальным выбором будет литье в силиконовые формы.
Безусловным лидером этого сегмента российского рынка являются наши клиенты — ООО «3Д Вижн». Для них специалистами «Современного оборудования» было поставлено и введено в эксплуатацию оборудование для аддитивного производства фирмы Stratasys: Objet30 Pro, работающее по технологии PoliJet, и Fortus 250mc, в которой использована технология FDM.
В «3Д Вижн» используют 3D-печать в первую очередь для прототипирования. О преимуществах 3D-печати в этой области написано уже немало. И мы, безусловно, рады, что наши клиенты используют правильные технологические решения.
Илья Виноградов, генеральный директор ООО «3Д Вижн», считает: «Прежде чем перейти к массовому производству изделия, имеет смысл изготовить его высокоточный прототип. Изготовление прототипа поможет вам в оценке внешнего вида изделия, дизайна, ведь одно дело рассматривать 3D-модель на мониторе компьютера, а другое — подержать ее в руках. Также вы сможете примерить все необходимые платы и датчики, что поможет вам избежать конструкторских ошибок. Прежде чем переходить к такому дорогостоящему этапу производства, как литье в пресс-формы, хочется быть уверенным, что на выходе получится изделие высокого качества. 3D-печать — это та самая технология, которая поможет вам избежать всех ошибок и неточностей».
Сегодня 3D-печатью для прототипирования уже никого не удивишь. А вот ее использование компанией «3Д Вижн» для изготовления оснастки второго порядка — это современный тренд в литьевом производстве. Какое же место отведено аддитивной технологии в, казалось бы, совершенно ином технологическом процессе?
В процессе литья в силиконовые формы три этапа:
1. Изготовление мастер-модели будущего изделия на 3D-принтере и, если необходимо, доработка ответственных поверхностей.
2. Изготовление силиконовой формы. Производится заливка силикона в форму с мастер-моделью и последующая ее выемка после разрезания получившейся формы.
3. Непосредственно литье пластика в изготовленную силиконовую форму, по необходимости специально разогретую, под давлением или в вакууме.
После заливки форма помещается в специальную камеру (термошкаф), где пластик застывает. В зависимости от используемого материала время полимеризации может составлять от 10 минут до 16 часов. С одной силиконовой формой можно получить от 10 до 50 изделий, после чего следует заменить ее новой.
В зависимости от особенностей изделия и пожеланий заказчика подбирают оптимальный моделирующий материал, отвечающий всем требованиям.
Изготовление мастер-модели является очень важным этапом, ведь качество отливок напрямую зависит от качества изготовленного прототипа. Именно поэтому в «3Д Вижн» огромным спросом пользуется печать из фотополимера по технологии PolyJet. Данная технология позволяет в короткие сроки изготавливать высокоточные прототипы, с поверхностью очень высокого качества, что позволяет тратить меньше времени на обработку лицевых поверхностей.
В «3Д Вижн» также активно использует установку Fortus 250mc. К несомненным плюсам этого 3D-принтера, работающего по технологии FDM, можно отнести точность построения, качество поверхности и, конечно же, стоимость печати. Печать из ABS-пластика на 3D-принтере Fortus 250mc. значительно дешевле, чем печать из фотополимера на Objet 30 Pro. Но на обработку лицевых поверхностей будет потрачено больше времени и средств. Поэтому необходимо вдумчиво подходить к выбору оптимального варианта оборудования для каждого конкретного производственного применения.
Если требуется печать крупногабаритных моделей, то «Современное оборудование» располагает промышленной установкой Stratasys Fortus 900mc с габаритами рабочей зоны 914×610×914 мм. Кроме того, на этой установке можно изготавливать прототипы и конечные изделия из различных термо-, химически стойких и высоко эксплуатационных пластиков.
Интересной особенностью является возможность использования растворимых пластиков для изготовления вымываемых сердечников. Процесс очень простой. Получив силиконовую форму, устанавливаем в нее закладной элемент. После того, как процесс литья завершается, сердечник просто растворяется в специальной ультразвуковой ванне, и вы получаете готовое изделие со сложными полостями.
Использование технологий 3D-печати для литья — это один из множества современных подходов, которые компания «Современное оборудование» предлагает своим заказчикам. Эти технологии успешно работают на отечественных предприятиях и уже не раз доказали свою высокую эффективность. Наши специалисты многократно доказывали это собственным опытом в реализованных проектах. В числе наших заказчиков в области аддитивных технологий — ОАО ААК «Прогресс», ОАО НИИ «Атолл», ФГУП «ЦАГИ им. Жуковского», ОАО НПП «Рубин», ООО «Сибирский арсенал», ОАО ЧНППП «Элара», ОА «ГосМКБ «Радуга», ОАО «КБХА», ООО «3Д Вижн» и многие другие высокотехнологичные компании.
Журнал «Умное производство», № 2 (38), июнь 2017, Евгений Гринин, группа компаний «Солвер», ООО «Современное оборудование».
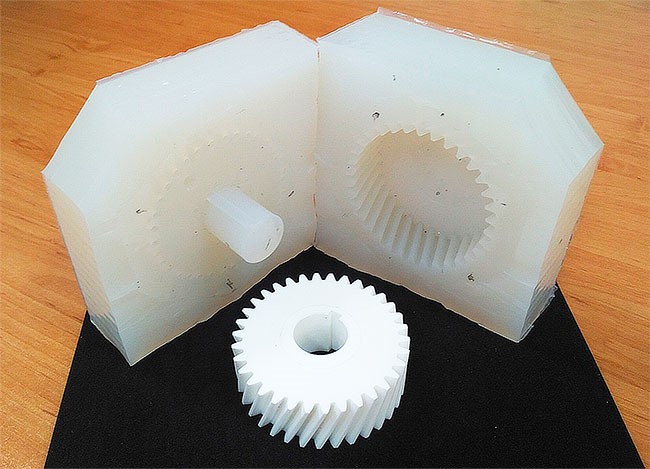
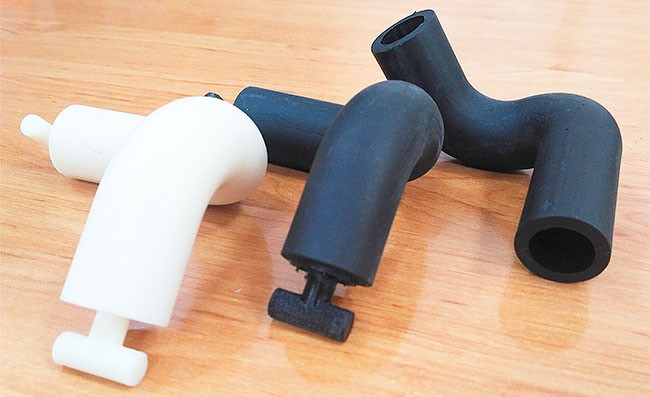